| 1988 | Osaka University, Faculty of Engineering, Graduated |
| 1990 | Osaka Univ., Graduate School, Division of Engineering, Master Course, Completed |
| 1990 | Saga Univ., Faculty of Science and Engineering, Research Associate |
| 1996 | Saga Univ., Faculty of Science and Engineering, Lecturer |
| 1998 | Saga Univ., Faculty of Science and Engineering, Associate Professor |
| 2005 | Saga Univ., Institute of Ocean Energy, Associate Professor |
| 2007 | Saga Univ., Faculty of Science and Engineering, Associate Professor |
| 2007 | Saga Univ., Institute of Ocean Energy, Associate Professor |
| 2007 | Saga Univ., Graduate School of Science and Engineering, Advanced Systems Control Engineering, Professor |
| 2007 | Saga Univ., Institute of Ocean Energy, Professor |
| 2010 | Saga Univ., Graduate School of Science and Engineering@Advanced Technology Fusion, Professor |
Research Field : Systems Control
Membership in Academic Societies :
Asian Control Association, IEEE, The Japan Society for Precision Engineering, The Robotics Society of Japan, The Institure of Systems, Control and Information Engineers, The Society of Instrument and Control Engineers
Our research interests are theory and practice of systems control. "Control" means the ability to manage a machine, vehicle, or other moving object (Oxford Dictionary of English). In particular, OTEC (Ocean Thermal Energy Conversion) plants and robots are the control objects of our research.
Please refer our laboratory's web site in detail.
OTEC (Ocean Thermal Energy Conversion) Plant Control
OTEC uses the temperature difference between cold (5-9℃) deep and warmer (25-30℃) surface seawaters to generate electricity (https://en.wikipedia.org/wiki/Ocean_thermal_ energy_conversion). Modelling and control of OTEC plants (Figure 1, Figure 2, Figure 3), and remote operation system (Figure 4) are developed.
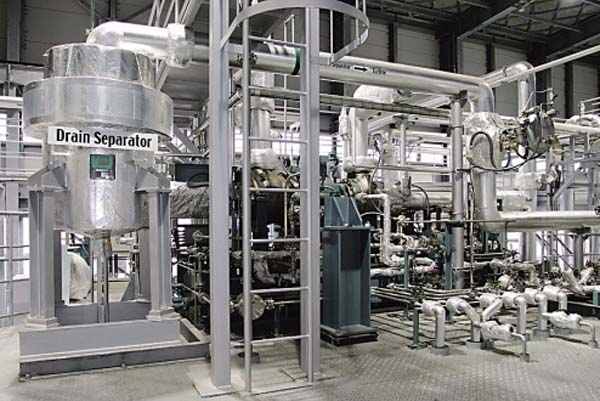
Figure 1 OTEC Experimental Pilot Plant in Institute of Ocean Energy, Saga University (https://www.ioes.saga-u.ac.jp/en/)
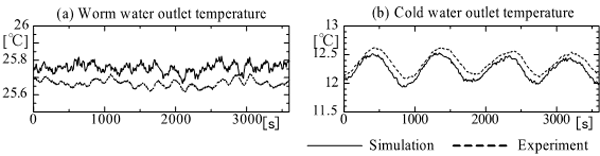
Figure 2 Simulation results by using OTEC simulation model.
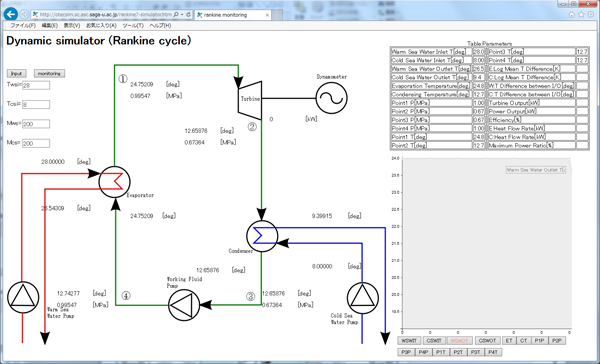
Figure 3 Dynamic simulator using OTEC simulation model.
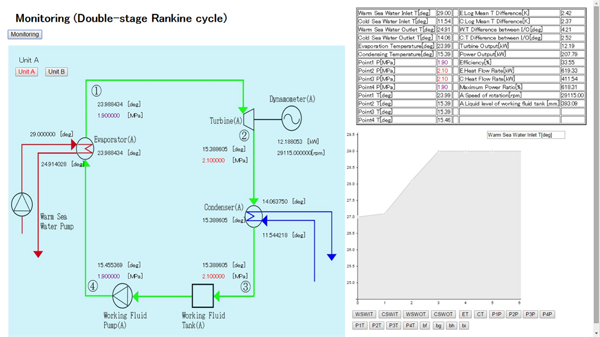
Figure 4 Remote monitoring system of an OTEC plant.
Robot Control
Mobile robot operation systems (Figure 5 and Figure 6) by using biomedical signals such as EMG (electromyogram) and EOG (electrooculogram) are developed.

Figure 5 Mobile robot operation system via biomedical signals.
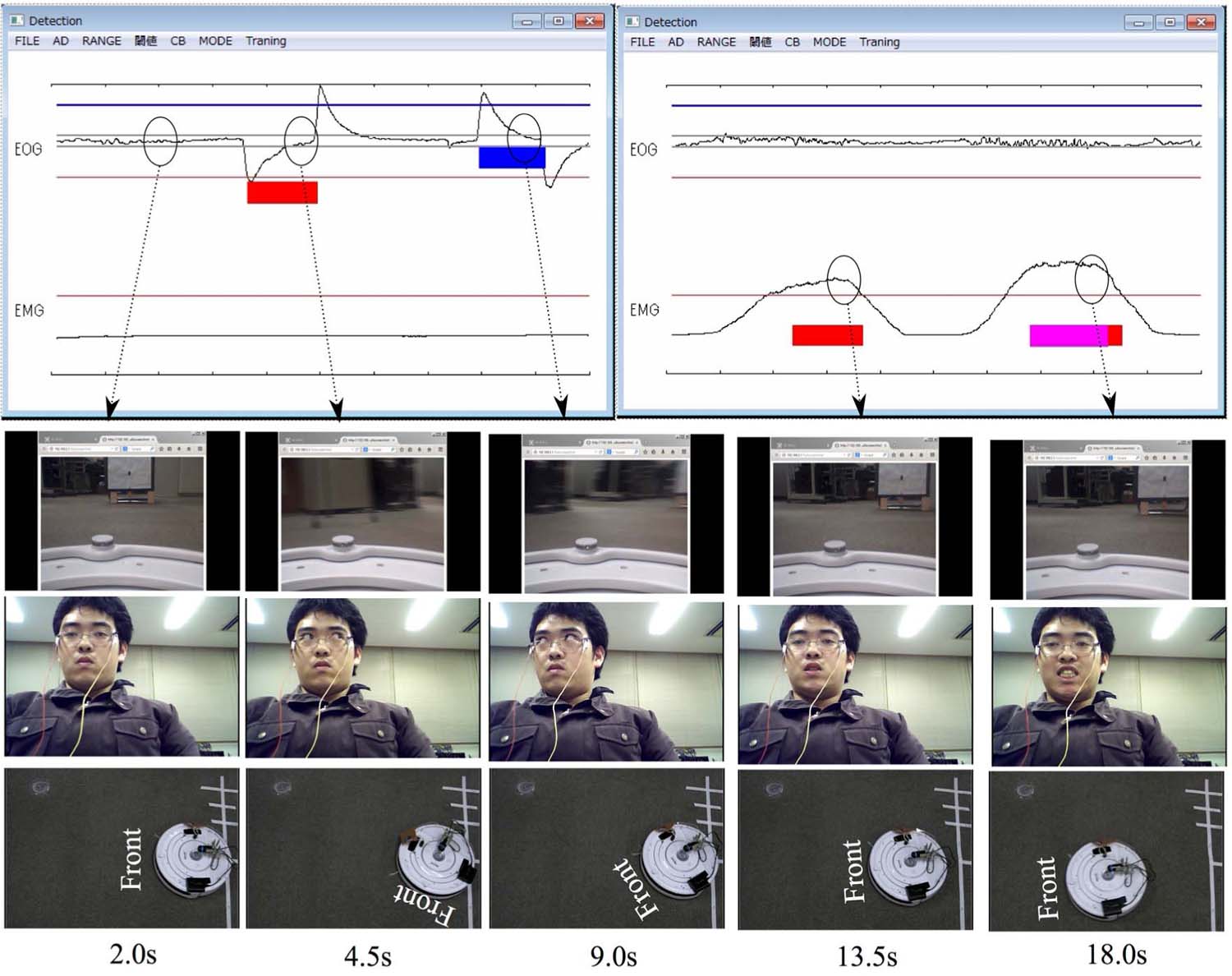
Figure 6 Experimental results of the mobile robot operation system.
|